AMF Enterprises
How to Extend the Lifespan of Hydraulic Cranes Through Fluid Analysis & Precision Calibration
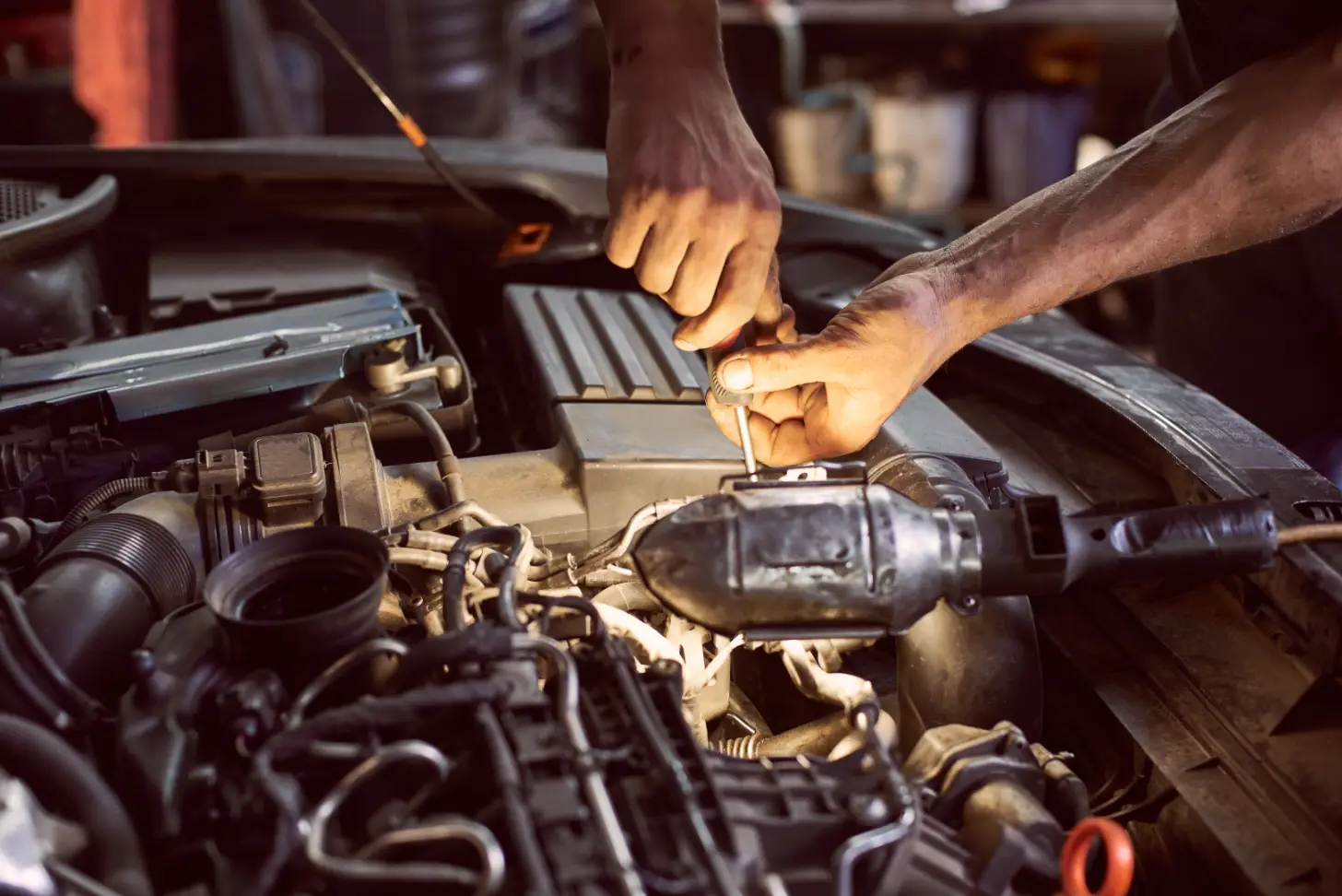
Maximizing Crane Performance Starts With Maintenance You Can’t See
Hydraulic cranes are the backbone of countless industrial operations—from construction sites and utility work to heavy equipment transport and fleet lifting. These machines endure high loads, extreme pressures, and repetitive motion every single day. But what keeps them functioning at peak performance isn’t just mechanical muscle—it’s what’s happening inside the hydraulic system.
At AMF Enterprises Inc, we’ve serviced dozens of cranes that failed not from sudden impact—but from internal wear caused by poor fluid health and miscalibrated valves or controls. The good news? You can prevent this. With routine fluid analysis and precision calibration, you can extend the life of your hydraulic crane, reduce downtime, and maintain lifting capacity with confidence.
Here’s how these two practices work—and why they’re essential to long-term crane health.
Why Hydraulic Systems Are So Vulnerable to Wear
Precision at High Pressure
Hydraulic cranes operate under pressures often exceeding 3,000 PSI. With such force coursing through hoses, cylinders, and valves, even minor contamination or misalignment can cause catastrophic failure. Internal components like spool valves, seals, and servo controllers are extremely sensitive to dirt, moisture, and incorrect fluid chemistry.
Repetitive Load Cycling
Each time a crane lifts, swings, or telescopes, it puts stress on its hydraulic circuits. Over time, these repetitive motions create internal friction and heat. Without clean fluid and proper flow calibration, that friction wears down seals, causes cavitation, and eventually leads to leaks, jerky movements, or complete cylinder failure.
What Is Hydraulic Fluid Analysis?
Fluid analysis is the process of collecting a hydraulic fluid sample and sending it to a lab for in-depth testing. The lab looks for signs of contamination, additive breakdown, water intrusion, and metal wear particles.
Key Indicators to Monitor
- Water Content: High water levels reduce lubrication and cause rust in steel components.
- Viscosity Index: Determines whether the oil can flow correctly at both high and low temps.
- Particle Count: Measures cleanliness levels based on ISO codes. High counts mean abrasives are in your system.
- Additive Depletion: Oil loses its anti-foam, anti-wear, and oxidation inhibitors over time.
- Metallic Wear Elements: Copper, iron, and chromium in the oil indicate pump, valve, or cylinder wear.
Why It’s Crucial for Cranes
Unlike engines, hydraulic systems don’t “burn” oil—it recirculates continuously. So if your fluid is dirty, it’s dirty all the time. You can’t afford to wait for failure to act. Routine fluid analysis gives you visibility into wear before performance drops or leaks develop.
How Often Should You Analyze Crane Hydraulic Fluid?
- Baseline: After 500 hours on a new crane or new oil
- Routine Monitoring: Every 250–500 operating hours
- Post-Repair: After a cylinder rebuild, valve swap, or major contamination event
- Before Oil Change: To determine if fluid is still serviceable or needs early replacement
At AMF Enterprises Inc, we include fluid sampling as part of our preventive crane maintenance packages—and use lab results to guide servicing and replacement intervals.
The Role of Precision Calibration in Crane Health
What Is Hydraulic Calibration?
Calibration involves adjusting flow rates, pressure relief settings, spool valve timing, and electronic sensor thresholds to match the crane’s manufacturer specs. Over time, components drift from their factory settings due to wear, vibration, or improper service.
Signs Your Crane Needs Calibration
- Jerky or erratic boom movement
- Delayed response during lifts or swings
- Load holding drift (cylinder slowly lowering)
- Hydraulic whine or unusual pressure spikes
- ECU or sensor fault codes related to hydraulics
Components That Require Calibration
- Load moment indicators (LMIs)
- Pressure relief valves
- Flow control valves
- Proportional control modules
- Electronic joystick and position sensors
- Boom angle and extension encoders
Calibrating these components ensures your crane operates smoothly, safely, and within load specifications. Skipping calibration can shorten system life and lead to unexpected safety lockouts.
The Power of Combining Fluid Testing and Calibration
These two services work best together. Clean, high-performance fluid ensures precision control is possible. At the same time, properly calibrated valves and sensors prevent your crane from overworking the hydraulic system.
Example: Cylinder Drift Solved
A customer’s crane was experiencing slow cylinder leak-down overnight. Initial assumption? A worn seal. But fluid analysis revealed high water content and low viscosity, which thinned the oil and bypassed tight clearances. Once fluid was replaced and pressures recalibrated, the issue disappeared—no cylinder rebuild needed.
Example: Jerky Boom Operation
Another crane showed jerky extension during boom travel. Fluid was clean, but calibration logs showed one valve solenoid reacting 50ms slower than the others. Recalibration restored smooth movement and prevented an unnecessary part replacement.
How to Set Up a Fluid and Calibration Program
Step 1: Baseline Testing
Start by pulling fluid samples from your crane's tank, filter return line, and any suspect cylinders. This establishes a health benchmark for future comparisons.
Step 2: Control Calibration Audit
Use diagnostic software or OEM tools to evaluate current valve timing, LMI readings, and electronic thresholds. Adjust any out-of-spec readings.
Step 3: Maintenance Scheduling
Set your fluid sampling and calibration intervals based on crane usage:
- High-use (daily): Every 250 hours
- Moderate-use (weekly): Every 500 hours
- Seasonal-use: Before and after deployment
Step 4: Record Keeping
Log all fluid results, calibration adjustments, and repair events in a shared system. Over time, this history helps identify performance trends and schedule proactive service.
Why Work with a Shop That Specializes in Crane Hydraulics
At AMF Enterprises Inc, we don’t just service cranes—we optimize them. Our team understands the hydraulic systems that power these machines and how fluid quality and calibration affect every lift, turn, and extension.
We offer:
- In-house and mobile fluid sampling
- ISO-certified oil analysis
- Factory-compliant valve and ECU calibration
- Post-repair testing and certification
- Load chart verification and safety reset services
With the right data, tools, and processes, we help you extend crane life and avoid mid-job breakdowns that hurt your timeline and budget.
Final Thoughts
Hydraulic cranes are precise machines that demand precise care. Clean fluid protects internal components. Accurate calibration ensures smooth, safe operation. Together, they form the foundation of a smart preventive maintenance plan.
If you rely on your crane to work under pressure—literally—don’t leave its future to chance. Partner with AMF Enterprises Inc to build a maintenance strategy that extends equipment life, enhances safety, and reduces total cost of ownership.